Best Industrial Robotics System
An industrial robot is a robotic system designed to perform different industrial tasks that are repetitive, dangerous, or unsuitable for human workers. These tasks include handling, welding, painting, palletizing, cutting, and finishing, among others, in a defined pattern to automate the production process in the manufacturing industry. Different types of industrial robots are available in the market, including articulated robots, Cartesian robots, cylindrical robots, SCARA robots, parallel robots, and collaborative robots.
Top 10 Industrial Robotics Vendors:
- ABB
- YASKAWA
- FANUC
- KUKA
- MITSUBISHI ELECTRIC
- KAWASAKI HEAVY INDUSTRIES
- DENSO CORPORATION
- NACHI -FUJIKOSHI
- SEIKO EPSON
- DÜRR
Overview
Industrial robots are designed to perform different industrial tasks, such as handling, welding, dispensing, processing, and inspection in a defined pattern to automate the production process. Industrial robots can be classified according to different criteria such as degrees of freedom, application, and design. In this report, industrial robots have been categorized into traditional industrial robots and collaborative industrial robots. Traditional industrial robots are used within cages or safety enclosures, whereas collaborative industrial robots are designed for use alongside workers and operators.
The industrial robotics market (excluding the prices of peripherals, software, and system engineering) was valued at USD 16.9 billion in 2018 and is expected to grow at a CAGR of 12.0% during 2019–2024 to reach USD 31.7 billion by 2024.
The competitive leadership mapping showcased provides information for the Industrial Robotics system. Vendor evaluations are based on two broad categories: product offering and business strategy. Each category carries various criteria, based on which vendors have been evaluated. The evaluation criteria considered under product offerings include the breadth of offering, delivery (based on industries that the vendors cater to, deployment models, and subscriptions), features/functionality, delivery, product quality and reliability, and product differentiation. The evaluation criteria considered under business strategy include geographic footprint (on the basis of geographic presence), channel strategy and fit, vision alignment, and effectiveness of growth (on the basis of innovations, partnerships, collaborations, and acquisitions).
Visionary leaders refer to the leading market players in terms of developments, such as product launches, innovative technologies, and adoption of growth strategies. These players have broad product portfolios and contribute heavily towards the overall robot shipment. They cater to most of the industries and regions worldwide. Visionary leaders primarily focus on their strong product portfolio, well-established brand equity and strong tie-ups with clients, integrators, and partners to stay ahead of the curve. For instance, FANUC (Japan) offers more than 100 types of industrial robots which include articulated, parallel, SCARA, cartesian, and collaborative robots. These robots have a payload capacity ranging anywhere from 0.5 Kg to 2,300 Kg. The company has a presence in around 108 countries and has sold more than 500,000 robots worldwide. A few other major players in this section include ABB (Switzerland), YASKAWA (Japan), KUKA (Germany), and Universal Robots (Denmark).
There are several companies in the industrial robotics market that largely offer robots catering to a specific use case such as painting and welding. They may also carter to a specific industry or segment. These companies leverage the functionality of their products for new or sometimes unconventional use-cases. Most of the dynamic players are classified under tier 2 and tier 3 companies, which have presence in various regions worldwide. Like visionary leaders, these companies also have tie-ups with clients, integrators, and partners. For instance, b+m Surface systems offer specialized articulated robots for various spray painting applications. These robots are explosion proof to prevent ignition and feature hollow wrists to eliminate paint contamination. They also feature an advanced drive and control technology for 158 high painting accuracy. The company targets major industries such as automobiles and electronics. Other players in this section include Dürr (Germany), IGM (Austria), Comau (Italy), and Yamaha (Japan)
The industrial robotics market is moderately dependent on innovators because of moderate capital requirement and less investment required for software development, and it is not very difficult for new players to enter this market. In addition, there is a high demand for these products; therefore, new players can make steady profits.
As the market poses a moderate threat to new entrants in establishing their footprint, there are several players providing industrial robotic systems to diverse clientele groups globally.
Industrial Robotics Market Dynamics
DRIVERS:
Growing demand for collaborative robots across all industry segments
Shortage of skilled labor in manufacturing industries
RESTRAINTS:
The high cost of deployment, especially for SMEs
Reduction of jobs due to automation
OPPORTUNITIES:
Increasing automation in the electronics industry
CHALLENGES:
Interoperability and integration issues with industrial robots
What are the major applications of Industrial Robotics?
Industrial robots are extensively used in manufacturing industries. They were initially used for simple material handling and spot welding tasks. As robots started to become more accurate, they were used for assembly tasks. With the introduction of SCARA robots, assembly applications were extended to small and delicate parts such as electronics. Further, with the introduction of parallel robots, material-handling applications were expanded. The addition of vision systems and force/torque sensors enabled grinding and milling applications as well as new welding applications such as arc and laser welding.- Owing to the high rate of adoption of industrial robots in the automotive industry for performing tasks such as moving vehicle bodies in assembly lines and mounting mechanical and electronic spare parts. Industrial robots are one of the key elements for automatizing processing tasks, which is expected to propel the growth of the industrial robotics market during the forecast period.
- The industrial robotics market for traditional robots, in terms of shipment, shows a trend similar to that of the market in terms of size for applications accounting for the largest market size and highest growth rate. However, the increasing adoption of traditional robots for simplifying the process of cutting in other industries such as wood and furniture is expected to fuel the growth of the market for the processing application.
- Industrial robots for assembly applications are deployed to ensure quality and consistency in manufacturing. The robotic assembly process requires speed and precision without compromising accuracy. Use cases can include assembling of automotive components such as engines and gearboxes, and even complex operations such as clutch plate assembly. These robots can also assemble small and intricate parts used in consumer electronics and medical devices that are nearly impossible to do by hand. Articulated, SCARA, and parallel robots are generally used for assembly applications.
- Welding automation offers numerous benefits, from improved productivity and consistency to minimize costs of production, labor, and materials. Complex welding processes that require highly skilled workers can be automated to repeatedly perform the same weld cycle.
- Gluing or sealing is a post-processing task. Robot-based gluing enhance part quality and reduces cycle time. This is achieved through high precision and consistency of glue application. These robots can achieve repeatability of 0.1mm. Without this accuracy, profits are diminished through cleaning and rework.
- For painting and finishing applications, specialized robots are used. The robot arm must be explosion-proof, which houses electrical control equipment. Thus, painting robots are constructed from lightweight aluminum so that there is no risk of ignition. Like welding robots, these robots also feature hollow wrists to eliminate paint contamination.
- Industrial robots are also used for food dispensing. Novel applications such as decoration or frosting are being programmed to be done by robots. The hygiene challenges inherent to dispensing liquid or semi-solid materials had prevented the widespread adoption of robotic technology.
- Grinding robots are used for quickly and efficiently processing parts of various objects such as vehicle bodies and wooden planks. These robots save time and costs while machining complex designs and at the same time improving the uniformity of each workpiece.
- Industrial robots are perfectly suited for automated inspection. Robots can inspect difficult to reach areas and can work in smaller footprints. Inspection can be performed both in raw materials as well as for finished parts. In the automotive industry, inspection is performed for holes, slots, trim, surfaces, and springs.
Industrial Robotics Market, By Type
Industrial robots are broadly categorized into 2 types; traditional industrial robots and collaborative industrial robots (alternatively known as co-bots or lightweight industrial robots). Traditional industrial robots are used within cages or safety enclosures, whereas collaborative industrial robots are designed for use alongside workers and operators. Industrial robots can be classified according to different criteria such as the degree of freedom, application, and design. For instance, articulated robots have more number of joints, which translates to a higher degree of freedom compared with SCARA robots. A painting robot needs to be explosion-proof and will require a greater reach, while an assembly robot requires shorter reach, but requires high speed and precision. Collaborative robots on the other hand often have a complex, curved design and integrated force sensors to minimize the force from impact as much as possible.
Traditional Industrial RobotsTraditional industrial robots are developed with speed and accuracy in mind. They are generally built to carry high payloads and are programmed to perform a single task continuously. They are well suited for high-volume production and have been fundamental in scaling up productivity in major industries such as automotive. These machines are dangerous in close proximity to humans and are generally deployed in a cage or an enclosure. They also require significant time for programming, especially in cases when multiple robots have to work in coordination with one another. Traditional industrial robots are further segmented into articulated robots, SCARA robots, parallel robots, cartesian robots, and others (cylindrical robots, spherical robots, and swing-arm robots). Other robots such as cylindrical and spherical robots are being slowly phased out.
Collaborative Industrial Robots
Collaborative industrial robots, also known as co-bots or lightweight industrial robots can directly and safely interact with humans in a shared workspace. These robots are not operated inside cages or safety enclosures. The ISO/TS 15066 standard on collaborative robots has been developed to define the robot’s maximum safe contact forces if it collides with a person. Thus, motion made by collaborative robots will not hurt humans even if they collide at full speed, due to their intrinsic safety features. Distinctive features of collaborative robots include rounded edges, embedded impact, and proximity sensors, as well as a lightweight design. Collaborative robots generally are of the same design as articulated robots, but there are a few other types as well.
Components of Industrial Robotic System
ROBOTIC ARM
A robotic arm generally consists of a mounting base, an arm, and a wrist. They are typically mounted to the ground or a workbench. They can also be mounted on the wall or in an inverted position on the ceiling. Some manufacturers design robots for alternate mounting, such as the IRB 910INV SCARA robot by ABB (Switzerland), which is specifically designed to be mounted on a ceiling. A robotic arm consists of different joints, which allow linear and circular motion. The number of axes in a robot generally depends on the type of robot.
END EFFECTOR
Also known as end-of-arm tooling, an end effector is one of the most critical components in a robotic system. It is attached to the wrist of a robot arm. Grippers, welding guns, and suction cups are some examples of end effectors that directly interact with the environment or object. However, there are some end effectors which are not necessarily installed on the endpoint of the robotic arm, such as tool changers and torque sensors, which rather function as an intermediary.
DRIVE
An industrial robot requires a drive system for moving its arm, wrist, and body. A drive system is generally used to determine the capacity of a robot. For actuating robot joints, three different types of drive systems are available—electric drive system, hydraulic drive system, and pneumatic drive system. Pneumatic drives are used in simpler robotic systems, whereas hydraulic and electric drives are used for heavier loads and increased precision. Robots with hydraulic drives are often unsuitable for cleanroom applications due to the risk of fluid leakage. The mechanism that drives a robot arm is termed as actuation. Hydraulic and pneumatic actuators are generally suited to driving prismatic joints since they produce linear motion directly. They are often referred to as linear actuators.
HYDRAULIC DRIVE
A hydraulic drive system uses hydraulic fluid and consists of a pump connected to a reservoir tank, control valves, and a hydraulic actuator. Hydraulic drive systems provide both linear and rotary motion. Hydraulic actuator drives have several advantages. They are not easily damaged when suddenly stopped while carrying a heavy load, can handle heavy loads on the end of the manipulator arm, can be used around highly explosive materials, and provide precise motion control over a wide range of speeds.
ELECTRIC DRIVE
Electric drive systems are capable of moving robots with high power or speed. An electric actuator drive commonly uses three types of motors—AC servo motors, DC servo motors, and stepper motors. Some manufacturers now offer robots that use direct-drive, frameless, or brushless motors, which eliminate some of the problems caused by AC servo motors, DC servo motors, and stepper motors. Robots that use direct-drive motors operate at higher speeds, with greater flexibility and greater accuracy than those that use conventional electric drive motors. These robots can meet the demands of advanced, high-speed, precision applications.
PNEUMATIC DRIVE
Pneumatic drive systems use air-driven actuators. The actuators drive work at high speeds and are most useful for small to medium loads. They are economical to operate and maintain and can be used in explosive atmospheres. Air is a free and readily available energy source. Hence, the installation of robots that use pneumatic actuator drives is easier and less costly than that of hydraulic robots. A pneumatic robot is a good choice for lightweight pick-and-place applications that require both speed and accuracy.
CONTROLLER
A controller allows for the programming of industrial robots. It consists of an operating system for interfacing and provision for real-time monitoring. Most industrial robot manufacturers also manufacture and provide their controllers for ease of programming and to minimize compatibility issues. The controllers should be capable of high-speed processing and should not only ideally support multiple robots, but also be capable of fast signal processing for image transmission from vision systems. Most controllers also have Ethernet and USB connectivity as standard.
SENSOR
Sensors allow an industrial robot to gather information about its environment. This information can be used to guide the robot’s behavior. The more complex a robot, the more the number of sensors used. A single task may require a combination of different sensors, or different tasks can be performed using a single sensor. Some of the sensors used in robotics are light sensors, sound sensors, temperature sensors, pressure sensors, proximity sensors, navigation/positioning sensors, and current sensors. Various position feedback sensors are used depending on the type of robot (articulated, SCARA, linear, or delta).
MOTOR
Modern industrial robots generally use brushless AC servo motors, but there are two other motors that are also used for industrial robots; stepper motors and DC servo motors. Stepper motors are used for robots where affordability takes priority. DC motors were extensively used in the early years of industrial robots. They provided robots with the ability to lift heavy items with a high degree of control for speed and positioning
Best Industrial Robotics
- Enterprise
- SME
- Startups
Industrial robotics is a robotic system designed to perform different industrial tasks that are repetitive, dangerous, or unsuitable for human workers. These tasks include handling, welding, painting, palletizing, cutting, and finishing, among others, in a defined pattern to automate the production process in the manufacturing industry. The industrial robots considered are broadly classified into 2 categories, traditional industrial robots and collaborative robots (co-bots). Traditional robots refer to robots such as articulated, SCARA, cartesian, parallel, and other robots.
360Quadrants forecasts the industrial robotics market to grow to USD 76 billion by 2024, at a CAGR of 9%. Growing adoption of collaborative robots and a shortage of skilled labor are the key factors driving the market growth. Increasing automation in the electronics space is expected to drive the growth of the industrial robotics market. Purchase and integration costs remain a prohibitive factor, restraining the penetration of automation, especially in small- and medium-scale industries.
Tech. advancements & decreasing costs are to drive the growth in the Industrial Robotics Market:
Top Industrial Robotics Companies - quadrant report identifies and benchmarks Top Industrial Robotics Companies such as ABB (Switzerland), YASKAWA (Japan), FANUC (Japan), KUKA (Germany), Mitsubishi Electric (Japan), and evaluates them on the basis of business strategy excellence and strength of product portfolio within the Industrial Robotics ecosystem, combining inputs from various industry experts, buyers, and vendors, and extensive secondary research including annual reports, company press releases, investor presentations, free and paid company databases. They are rated and positioned on 2x2 matrix, called as ‘Company Evaluation Quadrant’, and identified as Visionary Leaders ( Best Industrial Robotics Companies ), Dynamic Differentiators, Innovators, or Emerging companies.
The report includes market-specific company profiles of all 20 Industrial Robotics Leaders and assesses the recent developments that shape the competitive landscape of this highly fragmented market.
Top Industrial Robotics Companies - quadrant report identifies and benchmarks Best Industrial Robotics Companies such as Cognex Corporation (US), Basler AG (Germany), Omron Corporation (Japan), Keyence (Japan), National Instruments (US), and evaluates them on the basis of business strategy excellence and strength of product portfolio within the Industrial Robotics ecosystem, combining inputs from various industry experts, buyers, and vendors, and extensive secondary research including annual reports, company press releases, investor presentations, free and paid company databases. They are rated and positioned on 2x2 matrix, called as ‘Company Evaluation Quadrant’, and identified as Visionary Leaders ( Best Industrial Robotics Companies ), Dynamic Differentiators, Innovators, or Emerging companies.
SAMPLES:
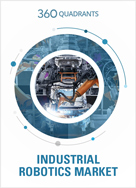
- Updated version of this Quadrant
- Different Company Evaluation Quadrant
- 'Startup Only' Company Evaluation Quadrant
- Region or Country specific evaluation
- Application or Industry specific evaluation ..Read More
- Submit a Briefing Request
- Question about our published research
- Request for evaluation of your organization for specific market
- Request for re-evaluation of Company Evaluation Quadrant ..Read More